In order to reach the desired performance of Ultra Racing products, we constantly monitor the quality of our products not only during the production stage, but also conduct strict performance testing afterwards.
During the development phase of Ultra Racing bars, we ensure the products are in accordance to our design and development philosophy. We conduct real on-road performance test as well as on-track testing. In order to obtain data, we also invented three testing jigs, namely Bending Test Jig, Torsion Test and Flex Test Jig: these jigs are used to test the performance of our products ona continuous basis.
The strut bar is bolted to the jig to simulate the actual situation on the vehicle chassis. For torsion test jig, torque is applied to one side of the bar, and the amount of twist is recorded. Torque used was calculated and fixed at 6.6kg/m.
Research & Development
For the compression test jig, forces are applied along both sides of the bar. Maximum compression force is recorded to study the structure of various kind of designs that the bar can withstand under different driving conditions including impact simulating an accident. We use a hydraulic pump to compress at set pressures and record the results
For flex test jig, torques are applied on the ends of the bars to simulate the performance of the bar under chassis flex conditions. Torque used for the experiment is fixed at 8kg/m.
Compression Test
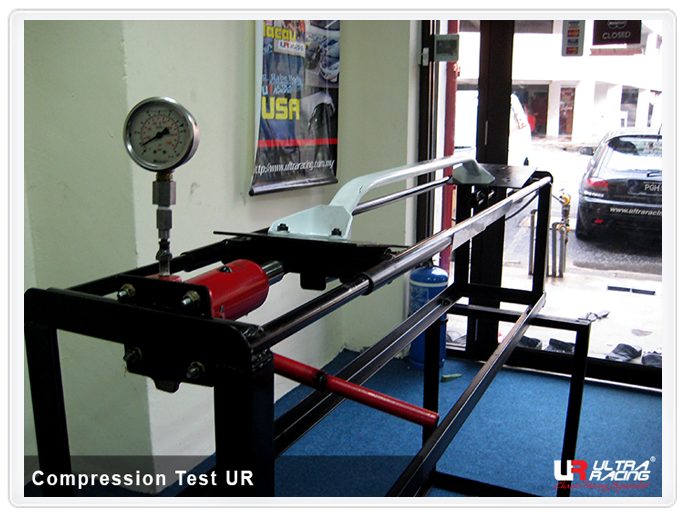
Brand : UR (Civic EK 2 points)
Bracket : Non Adjustable
Bracket thickness : 4mm
Weight : 1.5 KG
Commpression Impact : 3mm (100 psi)
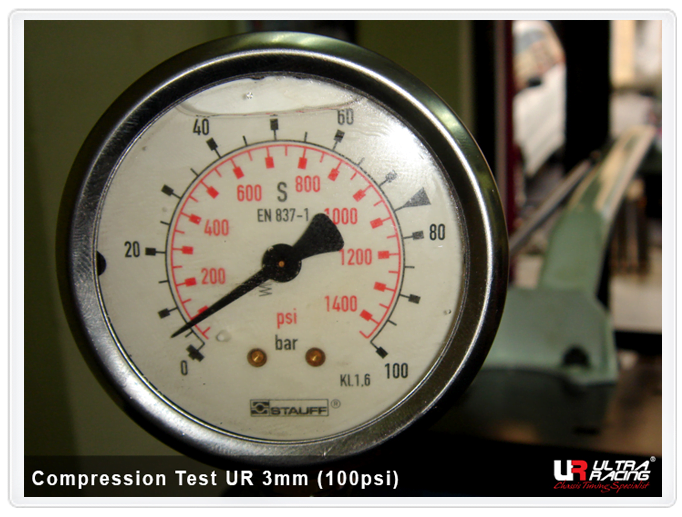
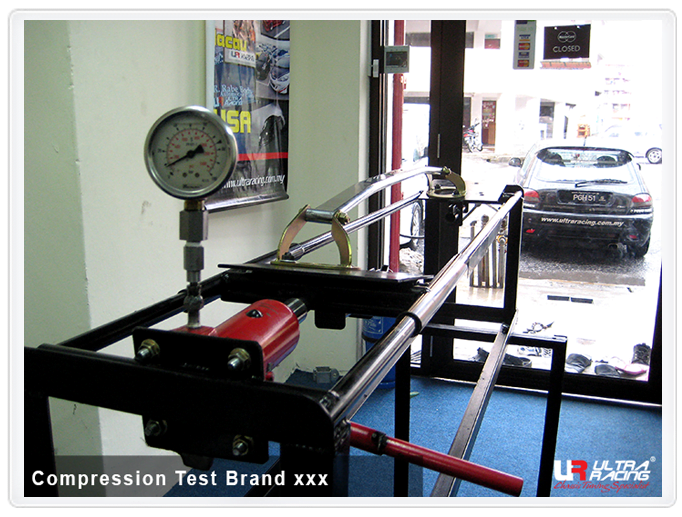
Brand : XXX (Civic EK 2 points)
Bracket : Adjustable
Bracket thickness : 4mm
Weight : 1.4 KG
Compression Impact : 70mm (100 psi)
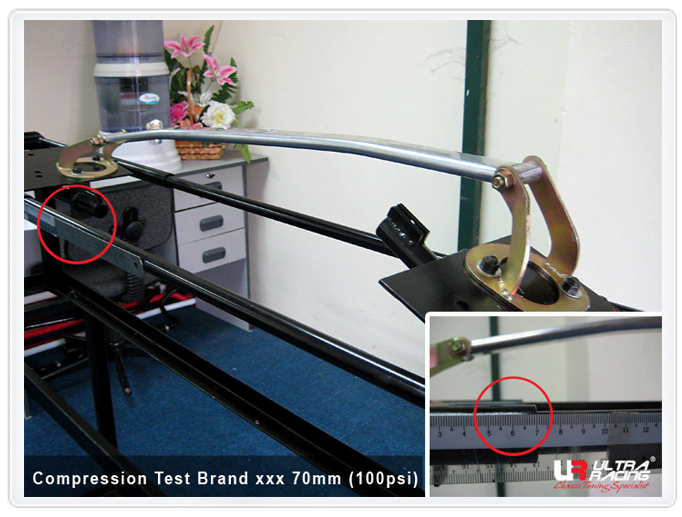
FLEX TEST
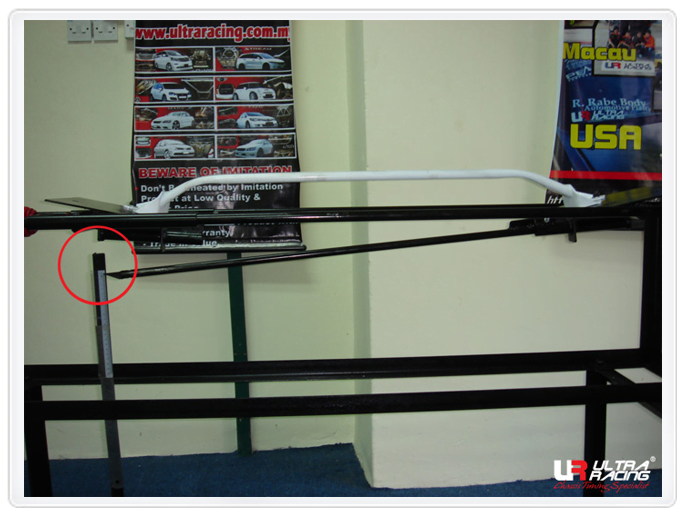
Brand : UR (Civic EK 2 points)
Bracket : Non Adjustable
Bracket thickness : 4mm
Weight : 1.5 KG
Flex : 50mm (8 kg/m)
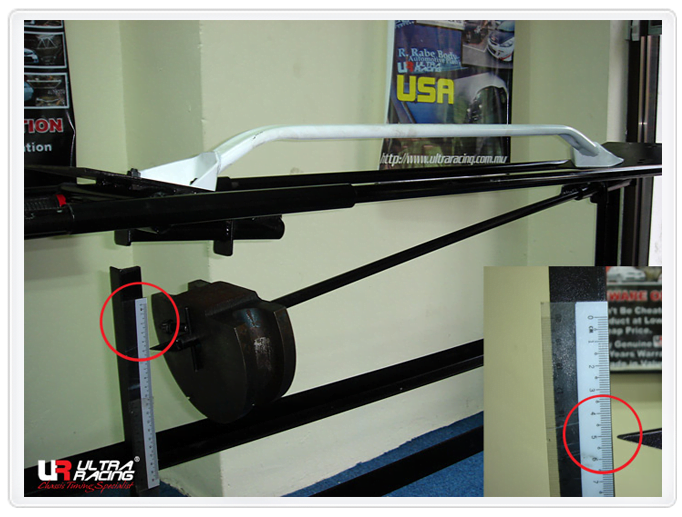
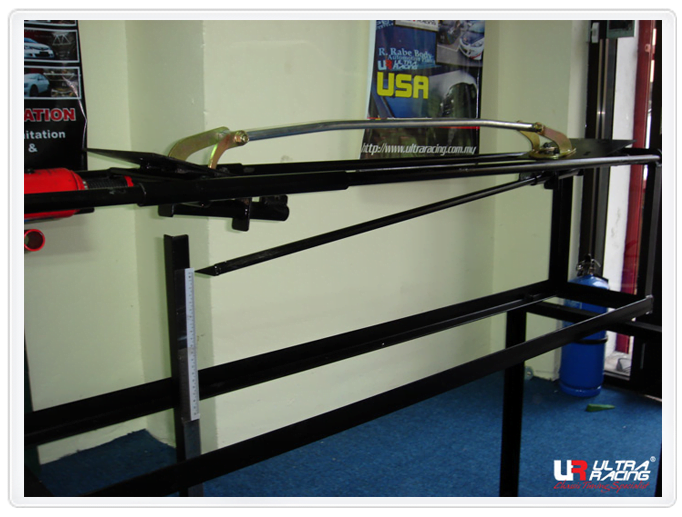
Brand : XXX (Civic EK 2 points)
Bracket : Adjustable
Bracket thickness : 4mm
Weight : 1.4 KG
Flex : ? (8 kg/m)
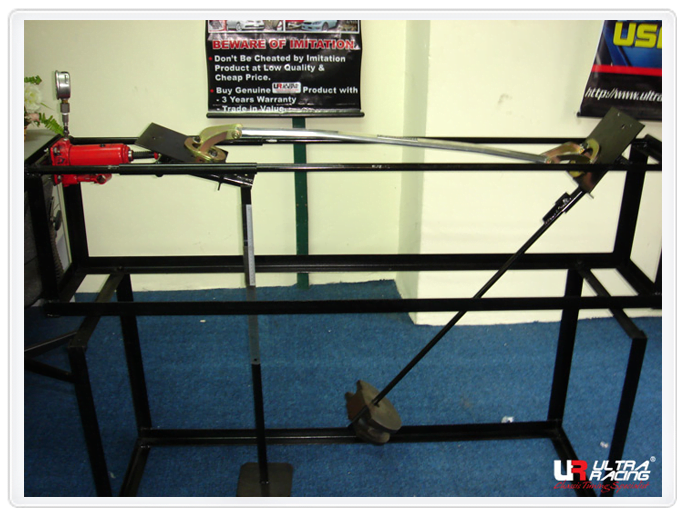
TORSION TEST
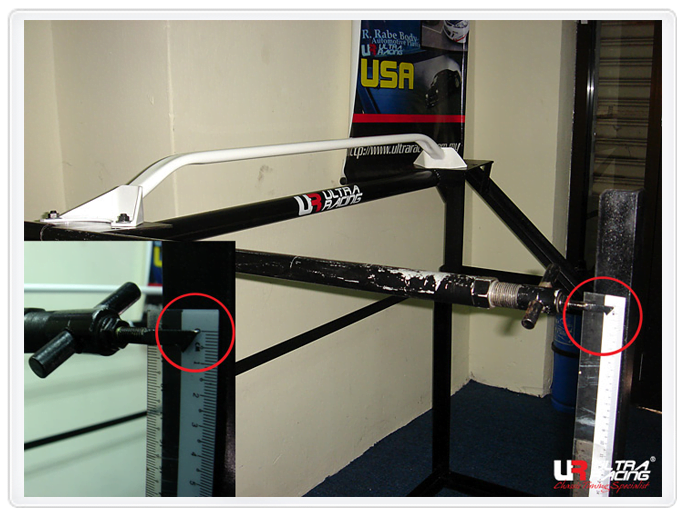
Brand : UR (Waja 2 points)
Bracket : Non Adjustable
Bracket thickness : 4mm
Weight : 1.8 KG
Torsion : 47mm
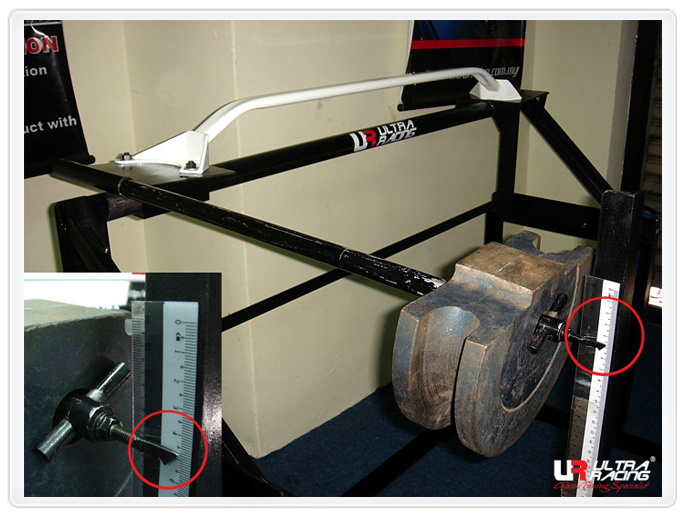
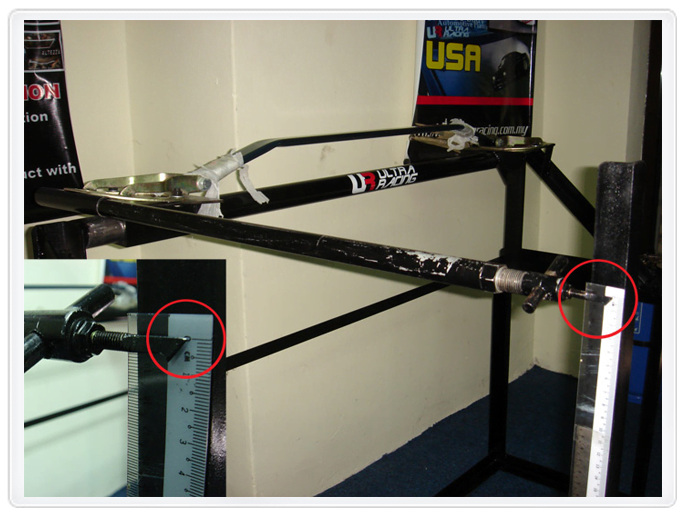
Brand : XXX (Waja 2 points)
Bracket : Adjustable
Bracket thickness : 4mm
Weight : 2.0 KG
Torsion : 85mm
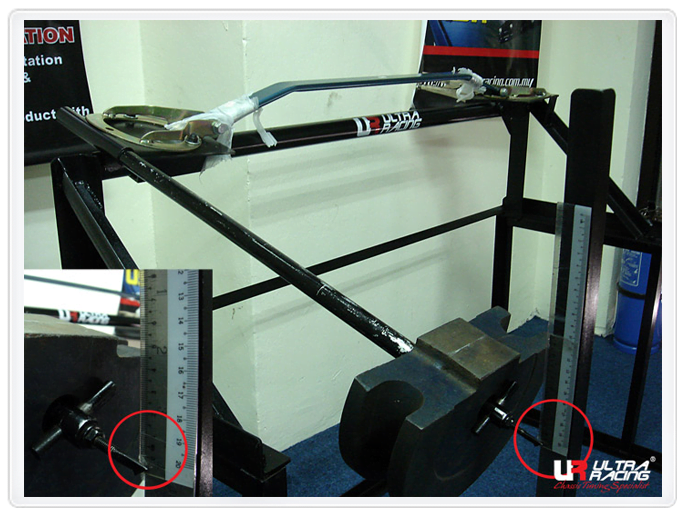
MATERIAL SPECIFICATION & DESIGN
Every materials used are carefully selected to ensure the best performance and safety. The brackets are made of 4mm to 5mm steel plates, while the hollow steel tubes and oval tubes are of 1.2mm to 1.6mm thickness. These materials are selected to ensure the bars are rigid and strong to maintain constant geometry at all times, yet safe enough to crumble during an impact for safety reason
All of our raw materials have been made and tested with satisfactory results.
To achieve safe condition, the displacement must be less than the thickness of the material which is below 2mm. Therefore, the bar is in SAFE condition.
MILL / TEST CERTIFICATE (Chemical Composition)
Specification
– JIS 3101 SS 400 (Japan International Standard)
– JIS G 3141 SPCC SD (Japan International Standard)
– ASTM A 500 Grade A (American Standard)
– BS 1387 ( British Standard)
STEEL VS ALUMINUM
Why we use Steel instead of Aluminum?
First, steel is stronger than aluminum for the same size and thickness. In order for aluminum alloys to be at least the same strength as steel, it has to be at least double the thickness (steel 4mm = aluminum 8mm). When that happens, weight saving is not so apparent anymore. Of course there are also exotic materials and alloys that can match the strengths of steel, but the cost are astronomically high and therefore not very cost effective to bring into mass production.